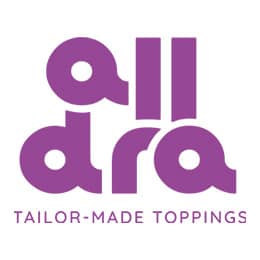
Alldra
Hoe krijgen we de productie, na een brand, zo snel mogelijk operationeel én gecertificeerd? Dat was de uitdaging waar suikerdecoratiebedrijf Alldra in 2016 voor stond. De oplossing: laat de nieuwbouw zo veel mogelijk gelijktijdig plaatsvinden met het opzetten en implementeren van een nieuw kwaliteitsmanagementsysteem.
Een hevige, uitslaande brand in de vestiging van Alldra in Rijssen legde op 20 mei 2016 het hele bedrijf plat. Bij de pakken neerzitten was er niet bij: “De keuze voor nieuwbouw was snel genomen, al tijdens het crisisberaad direct na de brand”, blikt het bedrijf terug. Alldra benadrukt het belang van het informeren en geruststellen van de afnemers: vanaf het begin tot en met de opstart van de productie: “Openheid van zaken geven is in zo’n situatie cruciaal. We leveren onze producten aan ijs- en bakkerijproducenten, snoepfabrikanten en aan co-packers voor de retailmarkt. Een deel van de productie konden we gelukkig tijdelijk uitbesteden. Zo gingen belangrijke leveringen toch door.”
Binnen twee weken vond Alldra in Almelo een geschikt bedrijfspand met een oppervlakte van 4.000 m2. Vervolgens heeft de organisatie alles op alles gezet om zo snel mogelijk de productie opnieuw te kunnen opstarten.
“Natuurlijk zonder concessies te doen op het gebied van kwaliteit en voedselveiligheid”, vertelt Q&A manager Tony Schoorlemmer. “Ondersteund door kwaliteitsadviesbureau KTBA slaagden we uiteindelijk met vlag en wimpel voor het behalen van het BRC7-certificaat.”
Het proces
Alldra is gespecialiseerd in de productie van suikerhagel, zachte- en harde musket (musketzaad). Voor de productie worden, voor een clean label, uitsluitend natuurlijke ingrediënten gebruikt. Er wordt ongeveer evenveel suikerhagel als zachte musket gemaakt: zo’n 1.000 ton per jaar, naast nog eens 1.300 ton harde musket. Tony Schoorlemmer vertelt over het proces: “Voor het musketzaad doseren we kristalsuiker in grote ronddraaiende open drageerpannen. Na toevoeging van suikersiroop voegen we voor harde musket zetmeel toe en voor zachte musket poedersuiker. Door het draaien vormen zich kleine ronde balletjes. Het drageren van een suikerkern tot een musketballetje neemt één tot anderhalve dag in beslag. Na het drageren volgt het kleuren van de musket in de ronddraaiende pannen. De hagel-installatie voor de suikerhagel wordt automatisch gevoed met een deegmassa van suiker, plantaardige olie en water. Na productie van het witte halffabricaat kunnen we alle mogelijke kleuren maken. Na het extruderen wordt de hagel gedroogd in een droogkamer.” Het was de droogkamer in Rijssen waar, door kortsluiting in de productie, de noodlottige brand ontstond. De schade was enorm: de hagelinstallatie ging geheel verloren, evenals een derde van de 200 pannen voor de productie en het kleuren van het musket.
BRC GS-norm in beeld
Voor de nieuwbouw in Almelo werd besloten om afdeling per afdeling te bouwen en deze gelijk schoon én productie gereed te maken. Om de productie zo snel mogelijk operationeel en gecertificeerd te krijgen, vond de implementatie van het kwaliteitsmanagementsysteem parallel aan de nieuwbouwwerkzaamheden plaats. “Het FSCC 22000-certificaat voor Rijssen was natuurlijk vervallen. Voor de nieuwbouw kwam logischerwijze de BRC GS 7-voedselveiligheidsnorm in beeld. Het was een prima moment om het kwaliteits- en voedselveiligheidsniveau van de productie naar een hoger plan te brengen”, aldus Schoorlemmer. Jacco Blenk, consultant bij kwaliteitsadviesbureau KTBA, verduidelijkt: “FSSC 22000 omvat richtlijnen waaraan het management op basis van risicoanalyse zelf invulling geeft. BRC GS geeft die ruimte in veel mindere mate. Deze norm is daarom bij uitstek een goede richtlijn voor het garanderen van de voedselveiligheid.”
Tony Schoorlemmer: “Door de gefaseerde opstart van de productie en door een strikte scheiding tussen nieuwbouwwerkzaamheden en productieruimtes te handhaven, zijn we erin geslaagd de kwaliteit en voedselveiligheid te borgen.”
Jacco Blenk: “Voortdurend werden er werkzaamheden afgerond of opgestart. Of er waren bijstellingen in het ontwerp, waardoor de documentatie aangepast moest worden.”
“Toch konden we zes weken na de brand al op een verantwoorde manier beginnen met de eerste productie van musket”, zegt Tony Schoorlemmer. “En de hagellijn, die geheel nieuw gebouwd moest worden, was al operationeel in november 2016.”
Hygiëne en routing
Bij het ontwerp van de nieuwe box-in-box fabriek in een – bij wijze van spreken – maagdelijk bedrijfspand, lag de focus op een zo hygiënisch mogelijke productieomgeving en een optimale logistieke routing. Het nieuwe pand bood hiervoor de ruimte. Er is ook plek voor een eigen opslagruimte voor eindproducten gerealiseerd en de inpakafdeling is zo ingedeeld dat er een houtvrije zone is gecreëerd. Marije Krabbe-Krejenzang, QA Technologist, geeft aan dat er afgescheiden ruimten zijn gecreëerd voor natte reiniging, acculaders en de stoomvoorziening. “In de productie is er daarnaast veel aandacht voor het voorkomen van allergenencontaminatie, vooral door het scheiden van de productie van harde musket enerzijds en zachte musket anderzijds. Heel belangrijk, want harde musket bevat immers zetmeel afkomstig van tarwe.”
Online kwaliteitsmanagementsysteem
Om de productie zo snel mogelijk operationeel en gecertificeerd te krijgen, vond de implementatie van het kwaliteitsmanagementsysteem parallel plaats met de nieuwbouwwerkzaamheden. Ook hierin lag een hele uitdaging. “Werkinstructies en procedures moesten aansluiten op de praktijk in het productiebedrijf” zegt Jacco Blenk van KTBA die Alldra hierin ondersteunde. “Voortdurend werden werkzaamheden afgerond of opgestart of waren er bijstellingen in het ontwerp, waardoor de procedures en documentatie aangepast moesten worden.”
Verbeteren van het ontwerp
KTBA keek mee met de ontwerpplannen en gaf zo nodig verbeteradviezen. “Meestal ging dat om details”, vertelt Blenk. “Zo ontdekten we bij het bekijken van de bouwplannen een deur die rechtstreeks toegang gaf tot de productieruimte. Daarachter was echter geen handenwasgelegenheid en geen schoeiselborstel. Dat zou aanleiding kunnen geven voor gebruik als sluiproute naar de productieruimte. Een ander voorbeeld was het advies een hekje te plaatsen bij de hygiënesluis, zodat medewerkers deze niet kunnen omzeilen op weg naar de productie. Hier bovenop kwamen de extra eisen vanuit BRC GS. De norm eist expliciet dat het hele kwaliteitssysteem van Alldra in de praktijk gevalideerd en geverifieerd is.” Een onderdeel van dit verificatieproces is het verificatieverslag en de managementreview. “Het volledige kwaliteitssysteem moest werkend in de praktijk bij Alldra beoordeeld zijn” zegt Blenk. “Het behalen van de BRC GS AA-status bevestigde dat het kwaliteitssysteem uitstekend werkte.”
Kwaliteitsbewustzijn
Kwaliteit en voedselveiligheid dagen Alldra voortdurend uit het beste van zichzelf te geven. “BRC GS legt in de fabriek de lat aanzienlijk hoger dan FSCC 22000” realiseert de QA-manager. “Belangrijk is nu vooral dat de operators meer aandacht besteden aan preventieve maatregelen in de productie, waardoor ‘correctieve maatregelen’ op den duur achterwege blijven. Medewerkers moeten elkaar bijvoorbeeld wijzen op geïmplementeerde hygiënemaatregelen, werken volgens de regels, en afspraken nakomen. Dagelijks hebben we daarom kwaliteitsoverleg: wat gaat er goed, wat fout, wat kan beter? We willen onze medewerkers deelgenoot maken van de productie, en als er problemen ontstaan, er samen voor zorgen dat ze die kunnen oplossen. Het kwaliteitsbewustzijn bij de operators is daardoor toegenomen. Uiteindelijk maak je kwaliteit op de werkvloer.”